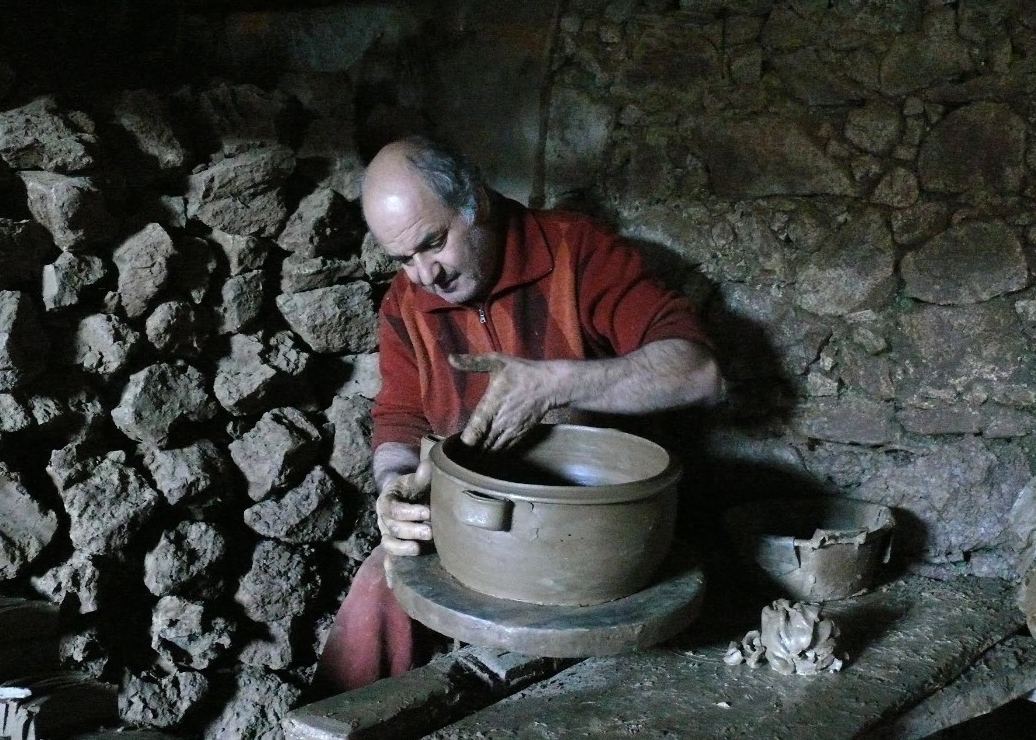
Located close to Soriano, Gerocarne is noted for the processing of clay for the production of fine domestic tableware. While production stopped in Soriano several decades ago, in Gerocarne the ceramics industry has continued from the sixteenth century to the present day. Despite the seismic events that have repeatedly destroyed the inhabited areas, traces of the ancient production structures still remain. The high number of examples located in close proximity to one another have led to the assumption that they acted as a fully functioning craft district.
Examination of the ‘catasti onciari’ land registers show that Soriano (1741), with its 65 'pignatari' style potters and two additional 'piattari' (plate makers), and the nearby Motta di Gerocarne, with a master potter, an 'argagnaro' (clay modeller), three rovagnari (tableware makers), two pignatari and three piattari, ranked among the most flourishing centres of the figulina ceramics tradition in Calabria at that time.
Soriano was also famous for the production of plates and jars used to store water, oil or cereal. The surnames of the artisans listed in the catasto onciario for Arena (1782) can even now be found among family groups engaged in these activities.
After the earthquake of 1783 in Soriano Alto, the piattari disappeared, moving over to the kiln production of Soriano Basso, which mainly focussed on jars, so much so that it became a point of reference for Catanzaro and the marquisate, and on rough containers for domestic use, such as amphorae.
Gerocarne distinguished itself in the production of tableware between the eighteenth and nineteenth centuries, and distributed its wares throughout a large part of Calabria Ulteriore. It also competed with Seminara in terms of its jugs and vases for preserving food, which were in great demand in the centres of the Plain.
Lenormant noted around 1880 that in Gerocarne “standard majolica vases are produced covered with a white tinned glaze, on which decorations are drawn over fire in various colours, including red, turquoise, green and yellow”.
The production of jugs continued in the small centre until after the mid-twentieth century, albeit with greater stylisation of the decorative motifs marked out horizontally along the shoulder, including the period when the Terracotta Group experimented with new forms.
Along with Seminara, Gerocarne is one of the historic centres of production in Calabria that has maintained the strictest continuity over time, passing down figulina art from generation to generation to keep the ancient wood kilns active, which they still are today, though they are now dedicated exclusively to the production of terracotta pottery for cooking.
Up to the 1970s, the potters in Gerocarne were divided into “whites” (known as ‘i jànchi) and “reds” (‘i russi), depending on the colour that the two different qualities of clay assume during firing and which formed the basis of their “art”. Their production methods were also highly distinct, and with them the “trade secrets”, the technical tricks that were indispensible for carrying out the work to the highest possible standards, and were furtively handed down from master to disciple.
As such, those who knew how to work with red clay struggled to work with the white clay, and vice versa, with few exceptions. The “whites”, who used the clay extracted near the town, which was calcareous, greyish, malleable and silky, mainly produced jugs with two symmetrical handles, known as cùccume, pots for storing in the larder and other tableware that was ingobed, glazed and refined with simple decorative motifs in copper green and rust yellow.
The “reds”, conversely, were specialised in the production of ‘pignata’ pots and pans of various shapes and sizes, using non-calcareous, oily, fire-resistant clay first extracted in Gigliari, above the town, then in the quarry in Rombolà in the Sant’Angelo region, which is still in use.
In the 1970s the lasts of the “whites” ceased their activities, once the market had evolved, replacing the traditional terracotta containers used in the home with more practical and “modern” industrial products made from plastic or glass.
At present, only the process for working the “red” clay survives in Gerocarne and it concentrates almost exclusively on the manufacture of cooking pans – tièji, tièsti and pignàti – with the addition of a few other shapes, such as bowls and pitchers.
Production
The clumps of clay extracted in Rombolà are kept indoors, stacked in a corner of the workshop.
After having ground them by beating them with a wooden mallet, which has now been largely replaced by a small mechanical crusher, the craftsman quickly passes the material through a sieve and puts the slightly coarser pieces to soak in a special masonry tank for around eight hours, keeping the pulverised part aside to adjust the consistency of the mixture before putting it into the mixer. This latter process used to be carried out without the aid of electrically powered machines.
Instead, the potters would trample and turn the clay with their feet, stretching it out on the floor, while for several decades now the mixer has made it possible to quickly produce homogenised and drawn material ready to be shaped on the potter’s wheel.
The processing takes place within the boundaries of a limited and standardised repertoire, following quick paced rhythms carried out almost in series, leaving little room for creativity.
A master potter needs only his eyes and the traditional shapes that he has imprinted in his mind to create a series of objects with practically identical dimensions. Once moulded, the pieces are detached from the turntable using an iron wire and put to dry in the sun or in the workshop, lined up on long wooden boards.
As soon as the items have dried to the right point, the throwing is completed by applying the handles. The first firing takes place in a kiln fuelled by broom branches. After a day of firing, the objects are taken out while still warm and moved to the storehouse before being painted and fired for the last time in a gas kiln.
The tools
Of the four kilns that miraculously still remain intact in the historic centre of Gerocarne, only one is still used by potters, and only for the first firing.
Gas or electric kilns are required for the second firing to ensure optimal fusion of the non-toxic paint. This has been used for crockery for decades now, replacing the “tin” that used to be prepared by the craftsmen themselves by grinding lead oxide with a stone found on site, which contained silica in addition to the metal oxides that gave the paint its characteristic yellow-orange colour.
The kilns typical of Gerocarne had large combustion chambers around 1.80 m tall, whereas the firing chamber was “constructed” by arranging the batch in a tapered pyramid formation, starting from the base of the wall, which was just 30-40 cm deep.
The kilns were not generally enclosed by building, but were rather covered by a large canopy with a single slope, known as a ‘pinnata’, leaning against one or two brick walls and supported by a system of wooden poles. The tiles level with the combustion chamber were replaced by metal sheets that could be removed easily during the firing process.
The batch is covered along the perimeter and on the top, using waste pans at the sides arranged with one placed sideways on the other, in parallel, overlapping lines. They are then stuffed with “straci” (rags) to fill the gaps, while the so-called “cima” (top) is mostly covered with plates and lids.
The items are loaded into the kiln when it is cold, usually with the assistance of family members, since it requires at least eight hours of work to properly arrange the load and coating in order to be able to begin the firing process.
The firing starts over a low heat. After approximately 20 hours, when all the residual humidity in the load has evaporated, the fire grows hotter and is fed at a sustained rhythm for at least four hours.
The potter observes the colour of terracotta used to cover the load, and when he is sure that the firing process has finished, the fire is no long fed and it is left to extinguish slowly. If rain is expected, the firing chamber is covered with metal sheets to prevent a thermal shock from harming the items.
By Camera di Commercio di Vibo Valentia